1. Hardware Failures and Component Degradation
PLCs and DCS systems rely on physical hardware that wears out over time. Harsh industrial environments accelerate component degradation. Dust, moisture, and temperature fluctuations further reduce lifespan. Regular inspections help detect early signs of failure. Proactive replacement of aging parts prevents unexpected downtime.
2. Software Compatibility and Firmware Updates
Legacy systems often struggle with modern software updates. Incompatible firmware can disrupt communication between devices. Engineers must verify version compatibility before upgrades. Proper documentation ensures smooth transitions. Testing updates in a controlled environment minimizes risks.

3. Cybersecurity Vulnerabilities
Connected control systems face increasing cyber threats. Weak passwords and outdated protocols expose networks to attacks. Regular security audits identify potential weaknesses. Implementing firewalls and encryption strengthens protection. Employee training reduces human-related security breaches.
4. Complex Troubleshooting and Diagnostics
Modern PLCs and DCS systems integrate multiple subsystems. Fault isolation becomes difficult without proper tools. Advanced diagnostic software speeds up problem identification. Clear troubleshooting protocols streamline maintenance workflows. Keeping detailed logs aids in future issue resolution.

5. Lack of Skilled Personnel
The demand for automation experts exceeds supply. Many technicians lack specialized PLC and DCS knowledge. Continuous training programs bridge skill gaps. Knowledge-sharing platforms improve team expertise. Hiring certified professionals ensures long-term system reliability.
6. Integration with Legacy Systems
Older equipment often lacks modern communication protocols. Retrofitting legacy systems requires careful planning. Middleware solutions enable seamless data exchange. Gradual upgrades prevent operational disruptions. Compatibility checks ensure smooth integration.
7. Ensuring Redundancy and Backup
System failures can halt production if redundancy is missing. Backup power and duplicate controllers enhance reliability. Automated failover mechanisms reduce downtime risks. Regular backup testing confirms data integrity. Redundant networks maintain continuous operations.
Conclusion
PLC and DCS maintenance presents multiple challenges. Addressing hardware, software, and security issues is crucial. Investing in training and diagnostics improves efficiency. Proactive strategies ensure long-term system performance. Staying updated with industry trends keeps operations running smoothly.
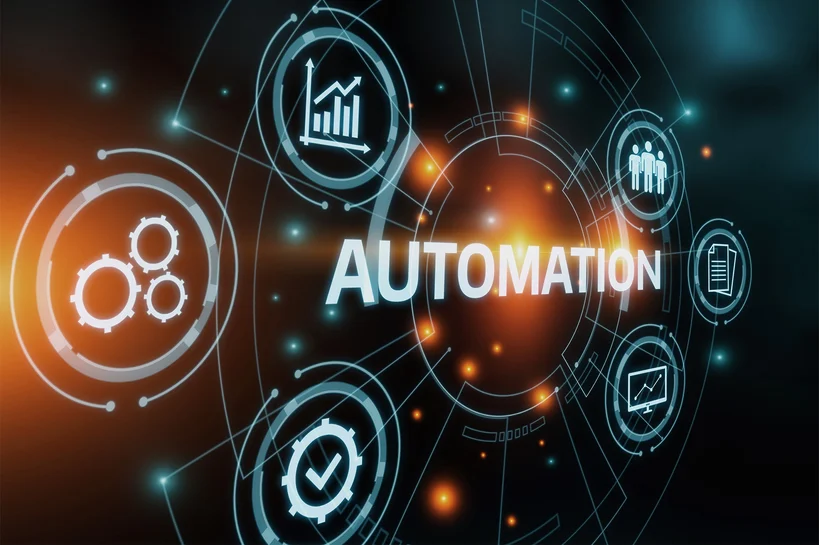
Check below popular items for more information in PLC Pioneer Limited.
Model | Title | Link |
---|---|---|
330103-00-08-10-01-05 | 330103-00-08-10-01-05 Proximity Probes Bently Nevada | Learn More |
330103-00-07-10-12-CN | 330103-00-07-10-12-CN Bently Nevada Proximity Probes | Learn More |
330103-00-07-10-12-00 | 330103-00-07-10-12-00 Bently Nevada Proximity Probes | Learn More |
330103-00-07-10-12-05 | 330103-00-07-10-12-05 Proximity Probes Bently Nevada | Learn More |
330103-00-12-10-01-05 | 330103-00-12-10-01-05 Bently Nevada Proximity Probes | Learn More |
330103-00-12-10-01-CN | 330103-00-12-10-01-CN Bently Nevada Proximity Probes | Learn More |
330103-00-05-10-11-05 | 330103-00-05-10-11-05 Bently Nevada Proximity Probes | Learn More |
330103-00-05-10-11-CN | 330103-00-05-10-11-CN Bently Nevada Proximity Probes | Learn More |